This week my wife asked me to try making these crazy geometric shelves! Plus we share a few of our favorite Maker Videos of the week!
Project of The Week!
This, is what my wife sent me earlier this week. Cool shelves for sure. And they look super simple right?
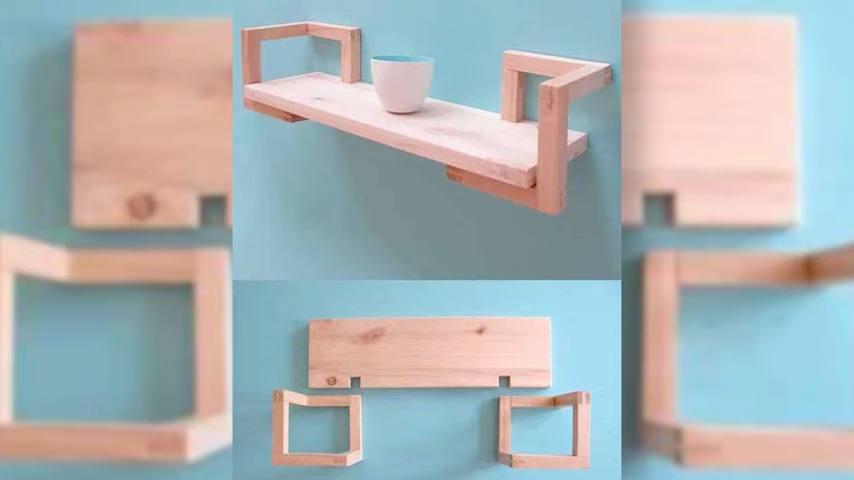
Well, to make sure those supports can, you know, support the shelf, it looks like they used bridal joints. So I tried that, using a handsaw, and uh, this is how the test piece came out. Not great. Not terrible, but not great. I built a full support and it was just, ugly. Too may imperfect joints.
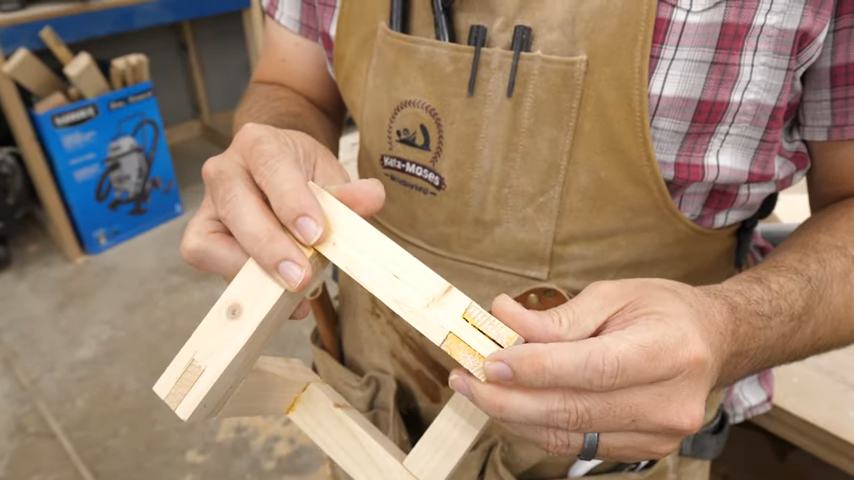
My wife wanted me to paint the supports black, so I knew the joints wouldn’t show. So to simplify this a bit, I decided to go with half laps.
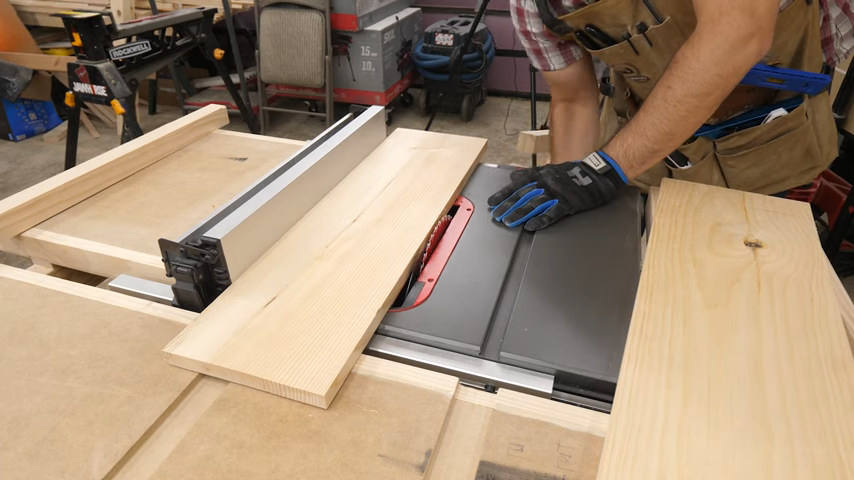
To determine how long to make my support pieces, I first needed to know how deep the shelves would be. In this case they’d be 7 and ¼”. I had a few pieces left over from my wife’s bookshelf, and I used those as a template to cut a third.
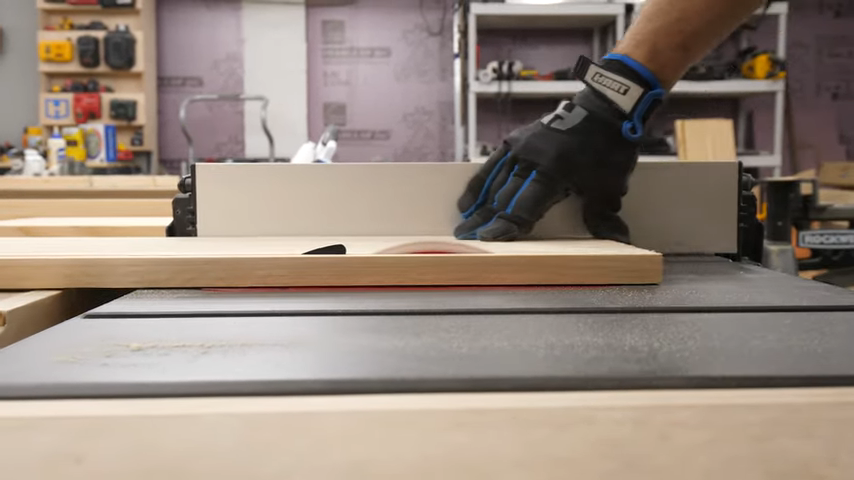
Next I used my sled to trim them to length.
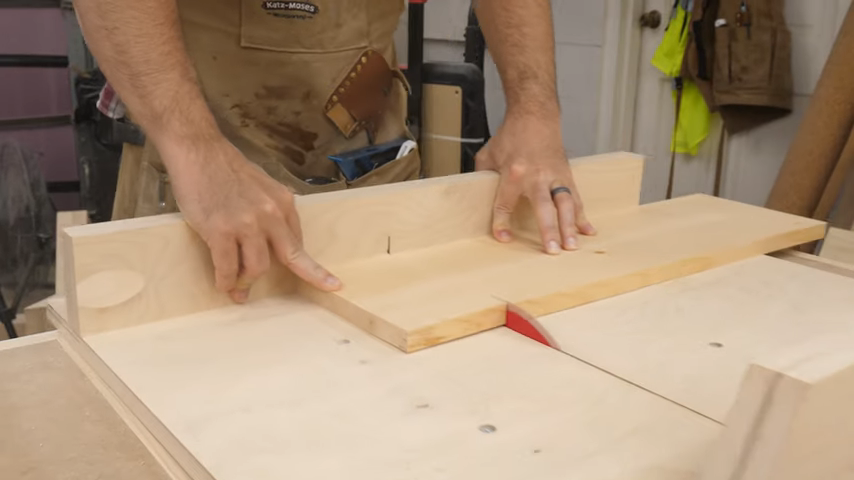
Next I needed to make the 1in square pieces that would make up the supports. I only had 2x2s so I cut them down on the table saw.
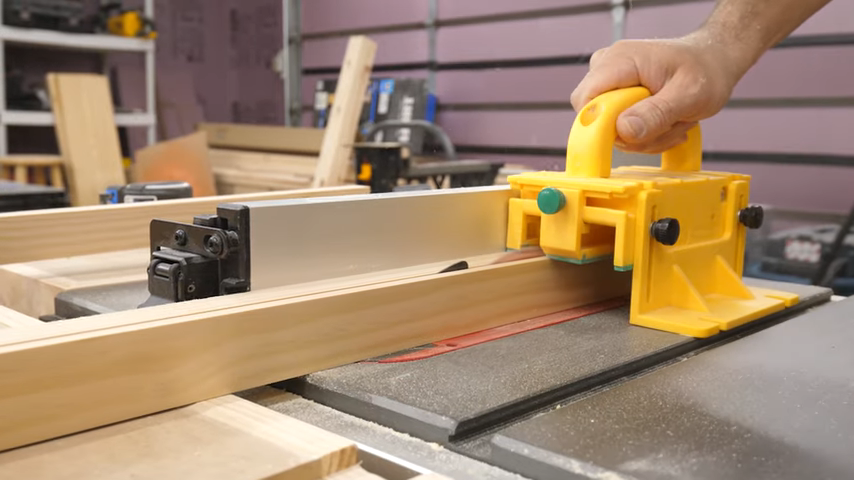
Once it was exactly 1” x 1”, I went back to the shelves to figure out how long my support pieces should be. I wanted the shelf to stick out a bit from the supports up front, so I decided to make them 6.5” each. I took it over to the mitersaw, setup a stop block, and cut all my pieces.
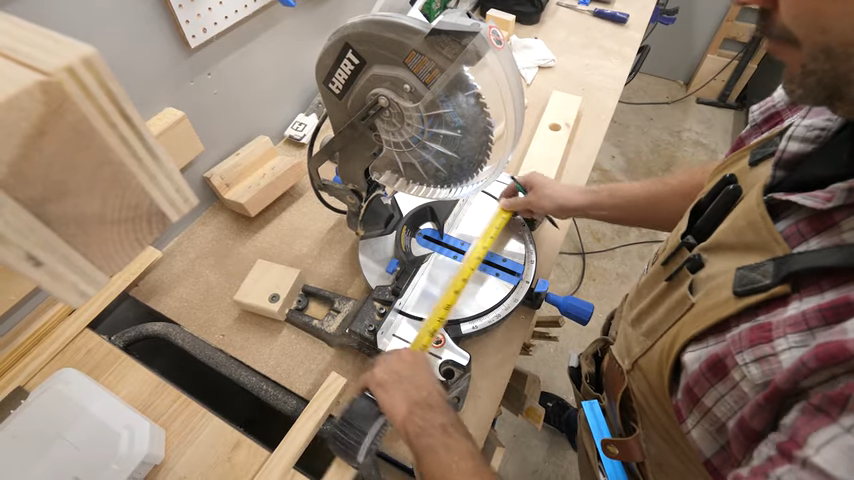
I was going to need 6 for each support, and made just enough for 1 shelf. I wanted to be sure this worked before I made the other two.
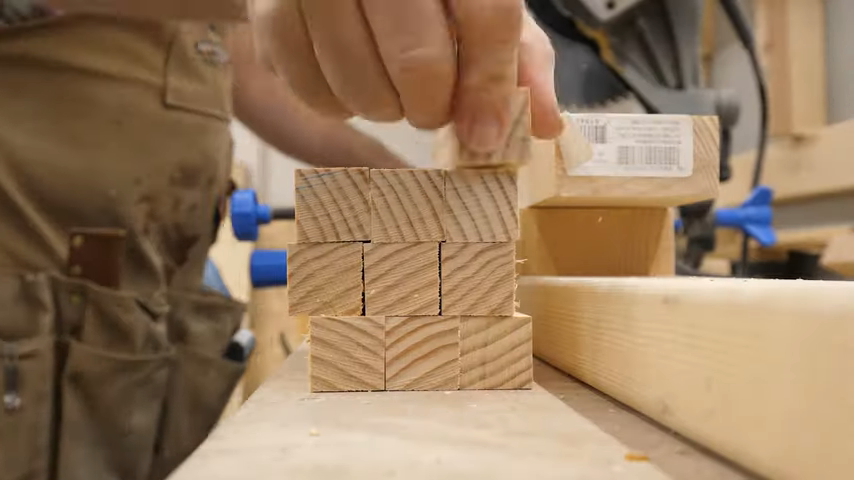
Once I had all 12 pieces ready, I had to figure out how these half laps would work. I realized that I could make 5 of the pieces exactly the same, as long as I flipped the last cut on the 6th one. You’ll have to trust me here, but that’s how the math worked out.
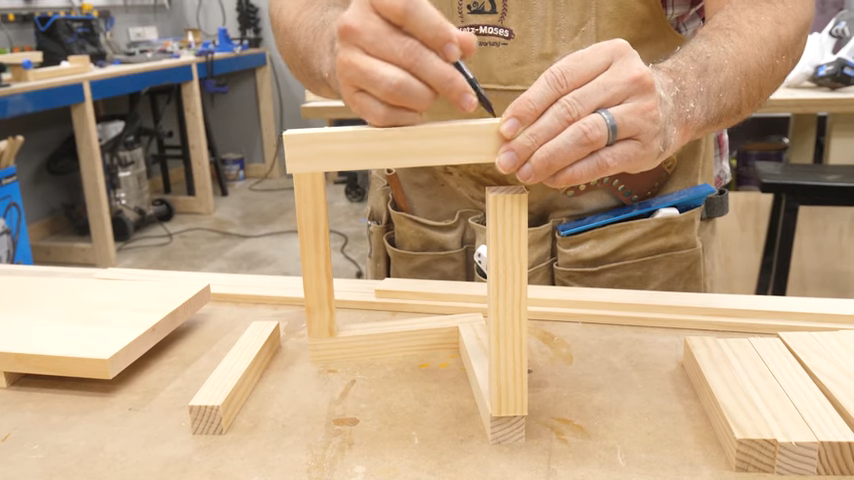
To cut all these half laps, Sarah suggested I use our sled to cut them out. So we tried a few test pieces and they fit great! So that’s what I did.
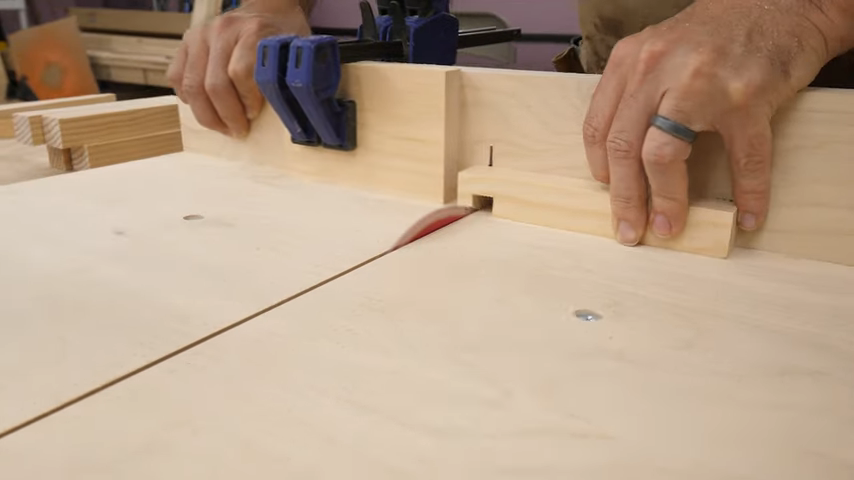
I clamped on a stop block to limit how deep I could cut, and then carefully adjusted the height of the blade to cut away exactly half of the wood. I wasn’t thrilled with how close my fingers were getting to the blade, but I had 10 when I was done.
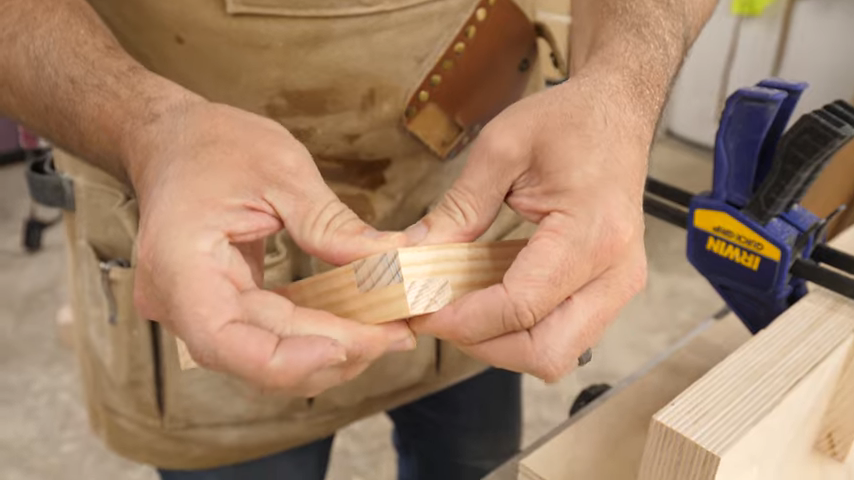
And look at that joint! So satisfying. I mocked up the pieces and they fit great. And as you could see, just the last one had to be cut differently on one end, and that made the whole thing work.
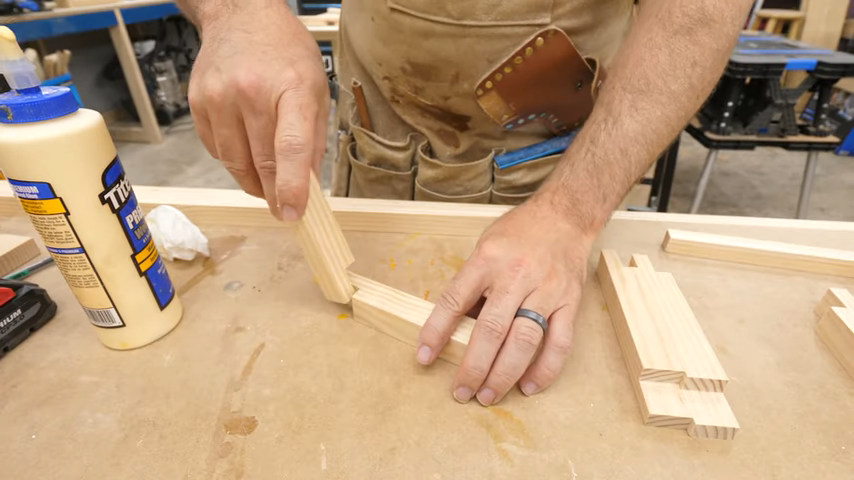
To hold these together, I used these two. Titebond II and my trusty brad nailer. The Glue would do the real work, while the brad nails held it in place while it dried.

I glued up each joint, pressed them together, and popped in a couple nails. Easy.
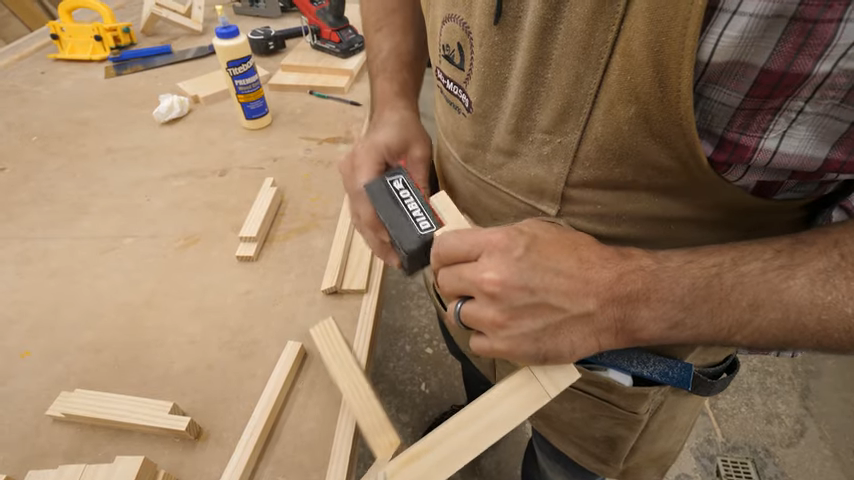
Some of the jointed needed a little sanding. When they did, I just grabbed my handy sanding block, and smoothed it over till it fit.
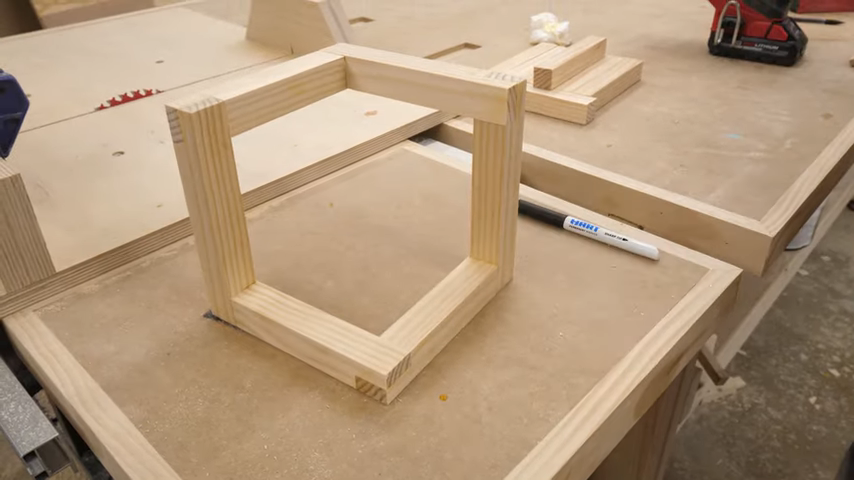
And there you have it! The joints are all tight, and strong. Now I just had to make 5 more. I let the glue dry over night, and then headed back in to paint and finish.
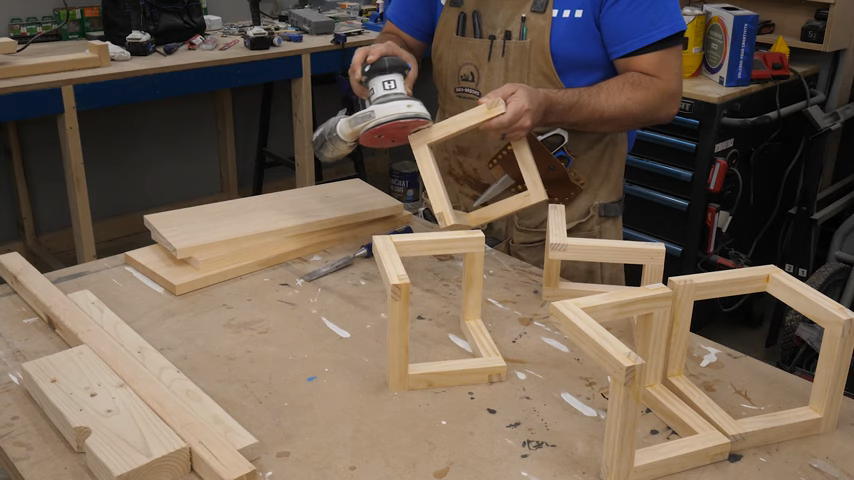
First I sanded each piece and chipped off any excess glue. I pulled out some paper to protect the table, got my pieces ready to paint. For the shelves I just used a water based poly, and the supports were painted black.
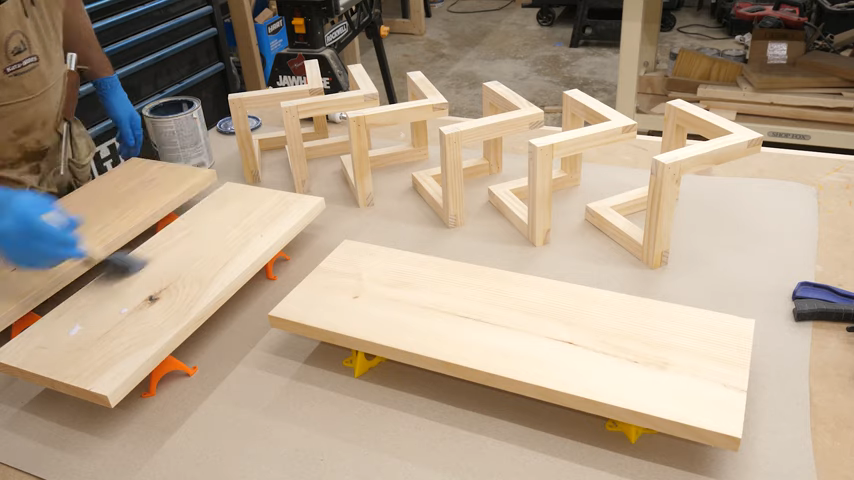
When they all dried, I remembered to cut out the notch in each shelf, nailed them together, and hung them up for my wife.
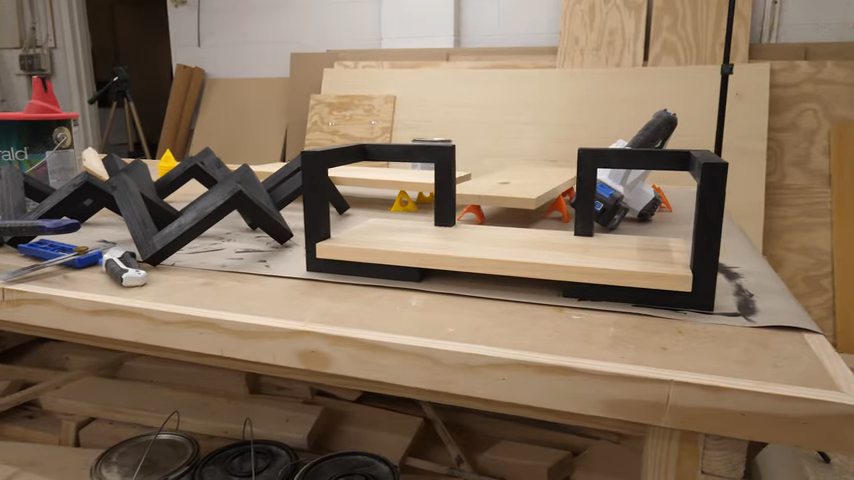
And there ya go. Once again, not a design I would have picked, but my wife knows what’s she’s doing, and sure enough, they look great when paired up with the other projects I’ve done for the living room.
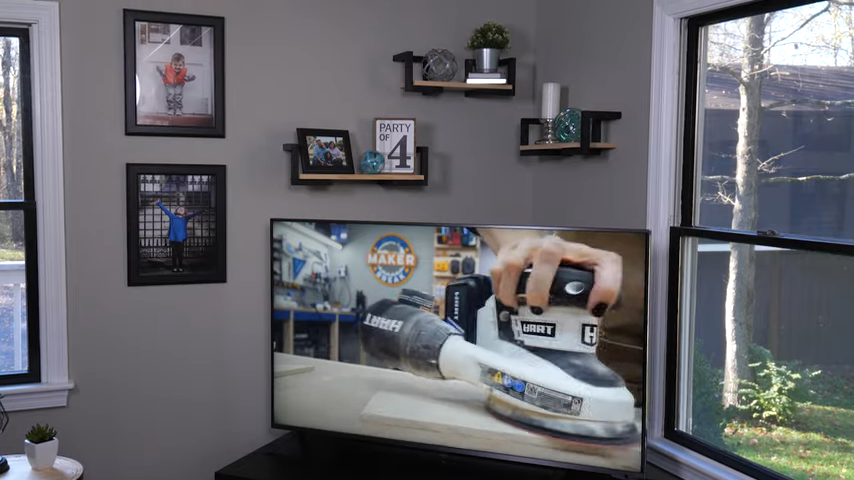
This project brought a lot of pain, but the reward was worth it.
Favorite Maker Videos of the Week!
First up, it’s almost Christmas! Over at LRN2DIY they’re getting a head start on Christmas, with permanent LED Christmas lights! This is NOT a cheap DIY project, but boy do I want to somehow fit this in my budget.
Mark Spagnuolo, the Wood Whisperer, shared a new product this week, called the Taper Maker, which is a jig for your table saw, to cut, well, tapers. But it was this last part that got my attention. YUP, it can be used in place of a jointer to flatten the edge of a board. As a guy without a jointer, SIGN ME UP. Mark has plans and a hardware kit for only $30, which I ordered. But I’m gonna have to figure out how to make the thing without several other high end tools I don’t have.
And last of all, Jay Bates built a set of adorable stairs… for his cat. Do I really need to further sell this video? Go watch it.